Welcome to

iFood360° is a new program, designed by Food Processing Skills Canada, to provide virtual reality learning experiences to people employed in the Canadian food and beverage processing industry and assist jobseekers and students in exploring new career opportunities.
“Virtual Reality is the next logical step in Food Processing Skills Canada’s mission to support people with the best skills development and training available. Not only is it a great alternative to hands-on learning when physical distancing is required but is also provides a safe and effective learning environment where students are immersed in the subject matter. “

Jennefer Griffith
Executive Director, FPSC
“Virtual Reality is the next logical step in Food Processing Skills Canada’s mission to support people with the best skills development and training available. Not only is it a great alternative to hands-on learning when physical distancing is required but is also provides a safe and effective learning environment where students are immersed in the subject matter.”

Jennefer Griffith
Executive Director, FPSC
iFood360° is creating 3 Streams of
Compelling Virtual Reality
Learning and Career Exploration Experiences
iFood360° is creating 3 Streams of
Compelling Virtual Reality
Learning and Career Exploration Experiences
Industry Specific Skills
Engaging activities on plant operations and food and worker safety, designed to enhance understanding and retention.
Social Emotional Skills
Immersive experiences on resiliency, empathy and adaptability, delivering new perspectives on social emotional skills.
Career
Exploration
Immersive adventures at food and beverage processing facilities and opportunities to view exciting careers in the industry hall of fame.
Why Virtual Reality?
Extensive research has shown that VR technology can safely deliver enhanced training benefits for learners compared with more traditional experiential learning.
VR training delivers a dramatic increase in learner confidence to perform trained tasks AND a significant reduction in on-the-job human errors.
VR also delivers risk-free training for potentially hazardous activities, reducing workplace injuries.
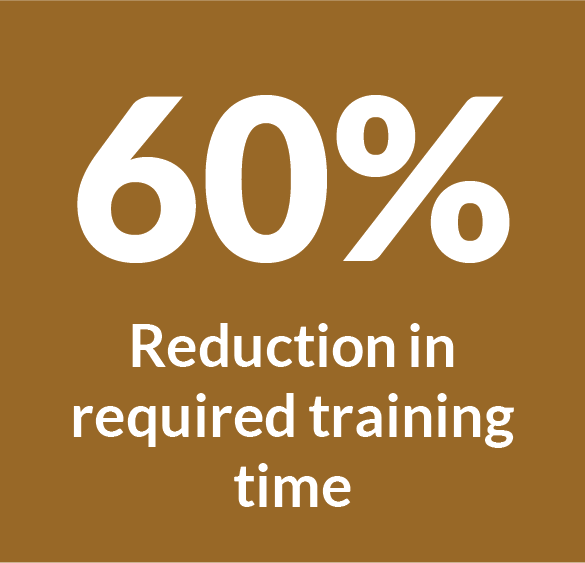
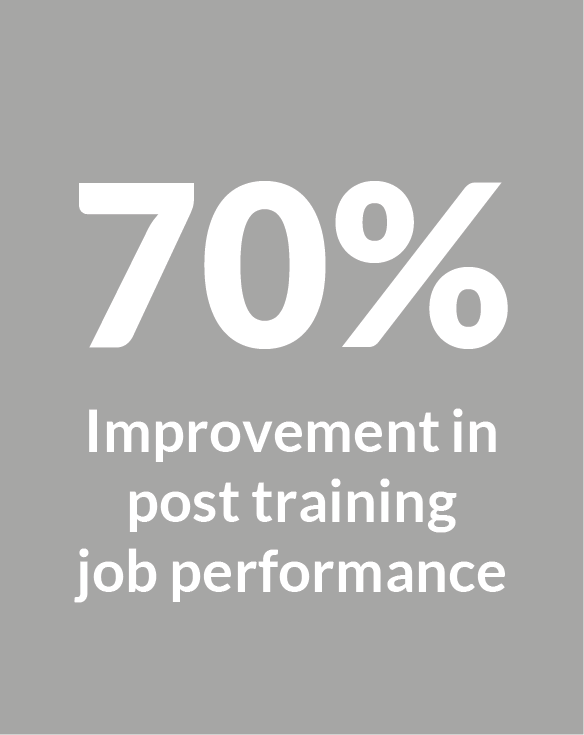
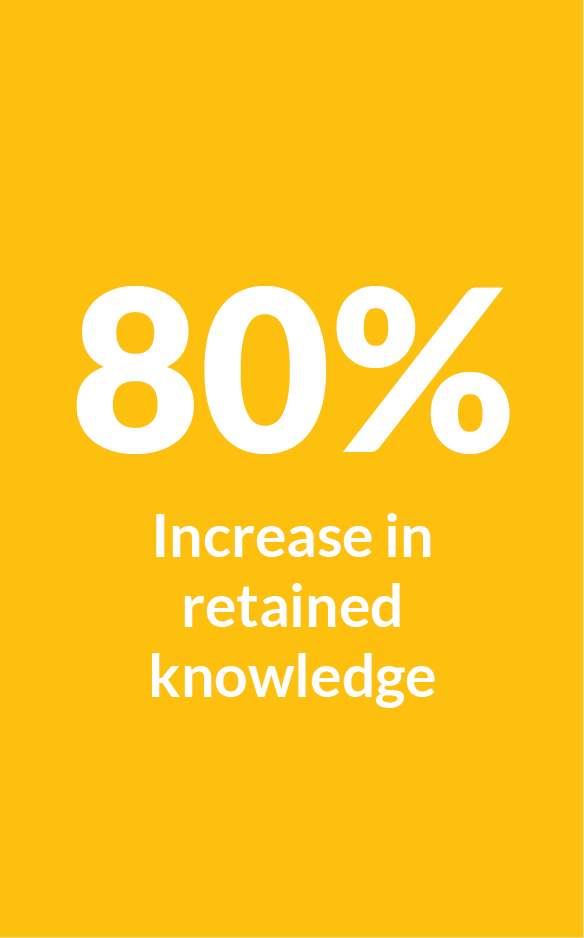
Want to learn more about VR?
FPSC has authored a research report on scalable virtual reality training options for small and medium sized enterprises (SMEs) in the food and beverage processing industry. The report examines studies of existing immersive technology implementations that have demonstrated significant measured improvements in areas like technical and safety training, soft skills development, productivity, and sales. It also offers guidance for our industry members on the current state of the technology and how they can implement virtual reality training solutions at a scale that is appropriate to their organization.
Want to learn more about VR?
FPSC has authored a research report on scalable virtual reality training options for small and medium sized enterprises (SMEs) in the food and beverage processing industry. The report examines studies of existing immersive technology implementations that have demonstrated significant measured improvements in areas like technical and safety training, soft skills development, productivity, and sales. It also offers guidance for our industry members on the current state of the technology and how they can implement virtual reality training solutions at a scale that is appropriate to their organization.
Equipment Downtime and Boost Productivity
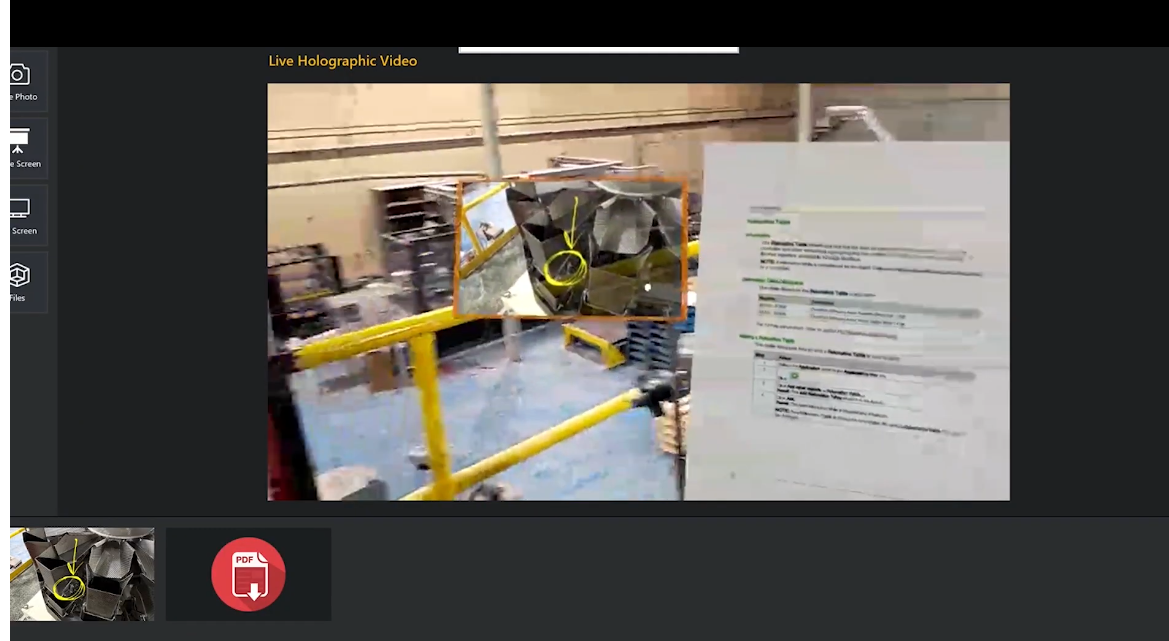
Located in St. Stevens, New Brunswick, Ganong Bros is a manufacturer of confectionary and chocolate items that occasionally faces critical downtime events due to equipment failure. Since their equipment comes from all over the globe, they traditionally rely on the original equipment manufacturers to come on-site to troubleshoot.
COVID-19 made their traditional approach nearly impossible due to travel restrictions. In order to solve this issue, they turned to the Microsoft HoloLens and a remote support application called Cognitive Spark. Rather than rely on sending cellphone videos, emails and voice calls back and forth to equipment manufacturers, the HoloLense allows Ganong Bros. employees to put on the device and remotely call technicians. Technicians can see exactly what the person wearing the headsets sees and they can quickly direct employees around the equipment, allowing them to drop multiple forms of media into the employee’s view to help them troubleshoot issues.
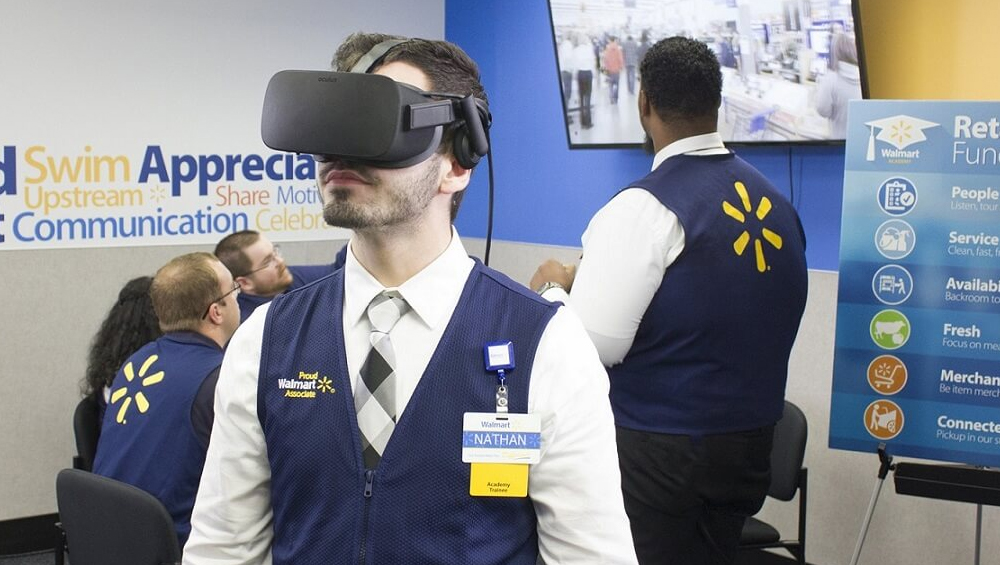
“The great thing about VR is its ability to make learning experiential. When you watch a module through the head-set, your brain feels like you actually experienced a situation. We’ve also seen that VR training boosts confidence and retention while improving test scores 10 to 15 percent – even those associates who simply watched others experiencing the training saw the same retention boosts.” said Andy Trainor, Walmart’s senior director of Walmart U.S. Academies.
Since 2017, Walmart has used VR for employee training and development through integration of the technology at Walmart Academies nationwide. Walmart uses VR to train associates in three main areas: new technology, soft skills like empathy and customer service, and compliance. This has been extremely successful, and the company now provides Oculus VR headsets to all stores in the U.S. to bring the same level of training to more than one million employees.
Uses VR to Safely Train Ground Crews
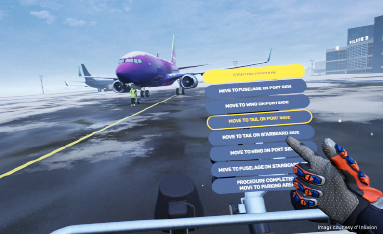
“The most effective way to learn is through experience. In live operations it’s very difficult to show people what can go wrong and how you can mitigate. Everything is smooth when operations are running in a very safe way. You don’t have the chance to show them what can go wrong...In the virtual environment, you can replicate error issues that we know exist in the industry and you can do it several times without affecting any real operations or any real equipment.” (Duhon & Trevino, 2020)
IATA developed RAMPVR, a VR technology to replicate real-life, high-risk scenarios in which people can learn safely. Participants were placed in a variety of scenarios to address operational issues such as foreign object debris and marshalling aircraft. In the marshalling module, trainees used VR controllers to perform the correct hand signals used on the tarmac. Using a neural network trained to understand these gestures, participants could signal to aircraft in VR and the aircraft would react as it would at the airport, enabling a new level of immersion in the training scenario.
Equipment Downtime and Boost Productivity
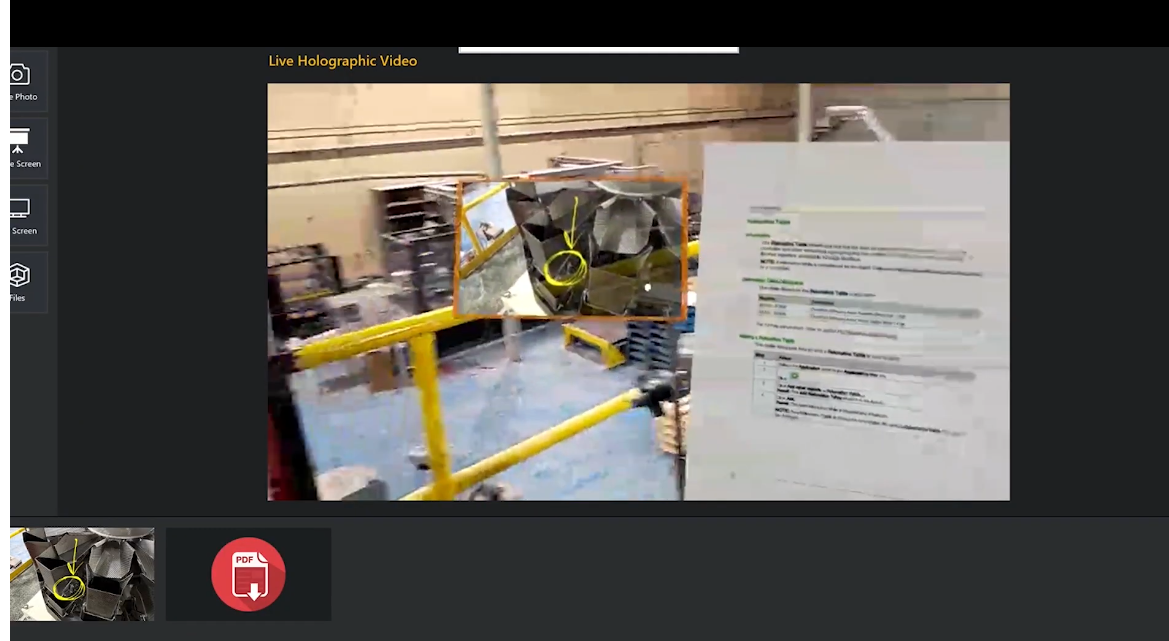
Located in St. Stevens, New Brunswick, Ganong Bros is a manufacturer of confectionary and chocolate items that occasionally faces critical downtime events due to equipment failure. Since their equipment comes from all over the globe, they traditionally rely on the original equipment manufacturers to come on-site to troubleshoot.
COVID-19 made their traditional approach nearly impossible due to travel restrictions. In order to solve this issue, they turned to the Microsoft HoloLens and a remote support application called Cognitive Spark. Rather than rely on sending cellphone videos, emails and voice calls back and forth to equipment manufacturers, the HoloLense allows Ganong Bros. employees to put on the device and remotely call technicians. Technicians can see exactly what the person wearing the headsets sees and they can quickly direct employees around the equipment, allowing them to drop multiple forms of media into the employee’s view to help them troubleshoot issues.
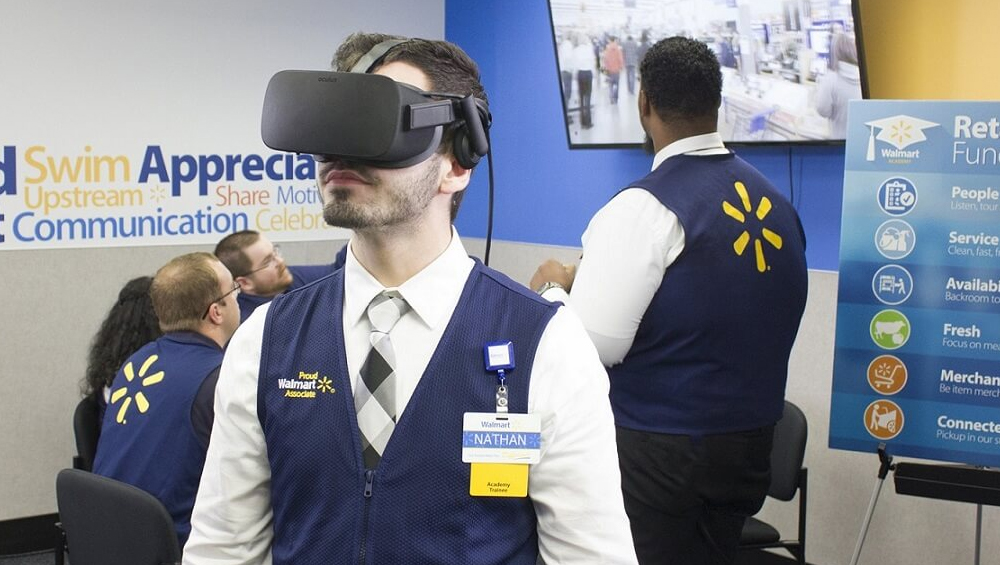
“The great thing about VR is its ability to make learning experiential. When you watch a module through the head-set, your brain feels like you actually experienced a situation. We’ve also seen that VR training boosts confidence and retention while improving test scores 10 to 15 percent – even those associates who simply watched others experiencing the training saw the same retention boosts.” said Andy Trainor, Walmart’s senior director of Walmart U.S. Academies.
Since 2017, Walmart has used VR for employee training and development through integration of the technology at Walmart Academies nationwide. Walmart uses VR to train associates in three main areas: new technology, soft skills like empathy and customer service, and compliance. This has been extremely successful, and the company now provides Oculus VR headsets to all stores in the U.S. to bring the same level of training to more than one million employees.
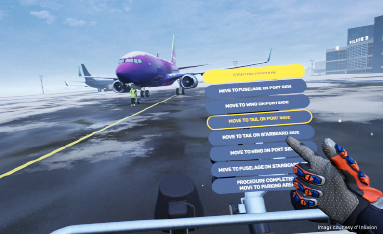
“The most effective way to learn is through experience. In live operations it’s very difficult to show people what can go wrong and how you can mitigate. Everything is smooth when operations are running in a very safe way. You don’t have the chance to show them what can go wrong...In the virtual environment, you can replicate error issues that we know exist in the industry and you can do it several times without affecting any real operations or any real equipment.” (Duhon & Trevino, 2020)
IATA developed RAMPVR, a VR technology to replicate real-life, high-risk scenarios in which people can learn safely. Participants were placed in a variety of scenarios to address operational issues such as foreign object debris and marshalling aircraft. In the marshalling module, trainees used VR controllers to perform the correct hand signals used on the tarmac. Using a neural network trained to understand these gestures, participants could signal to aircraft in VR and the aircraft would react as it would at the airport, enabling a new level of immersion in the training scenario.
Interested in being our virtual reality training partner?
We are inviting Canadian food and beverage processors to partner with us in delivering transformative social-emotional and industry-specific operational training to employees using exciting and new virtual reality technology.
We are also inviting educational institutions, community employment associations, and immigrant serving organizations to partner with us in offering career exploration opportunities to jobseekers and students using exciting and new virtual reality technology.
How It Works
Are you an Educational Institute, Community Employment Association, or Immigant Serving Organization?
How It Works
Are you an Educational Institute,
Community Employment Association, or
Immigant Serving Organization?
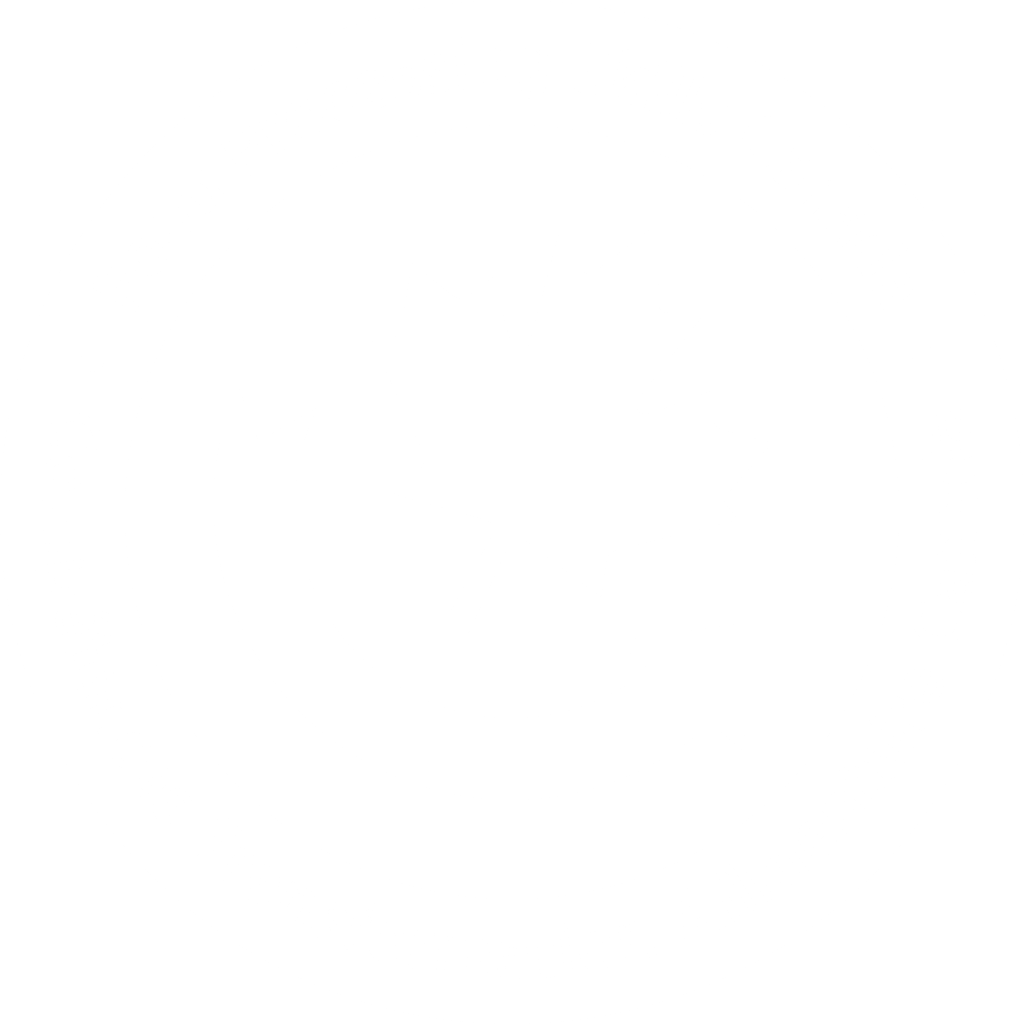
For the latest workforce development and planning information sign up for FPSC’s free newsletter